Following manufacturing onboarding best practices isn’t just a good idea—it’s a legal and financial necessity. According to the National Association of Manufacturers, manufacturing is one of the nation’s most regulated industries, with the government issuing more than 6,000 new final rules in 2021 and 2022 alone.
Inadequate onboarding puts your business at higher risk of noncompliance with labor standards and safety protocols. The result? Hefty penalties, lawsuits, and worker’s compensation claims—all expenses you can avoid with proper training. As of 2025, a single OSHA violation costs companies up to $16,550.
Given all the regulations and financial risks involved, the employee onboarding process is the perfect time to get team members settled into their new work environment from day one. To tackle this successfully, you need to know what makes an onboarding process effective and how to implement one across different manufacturing environments.
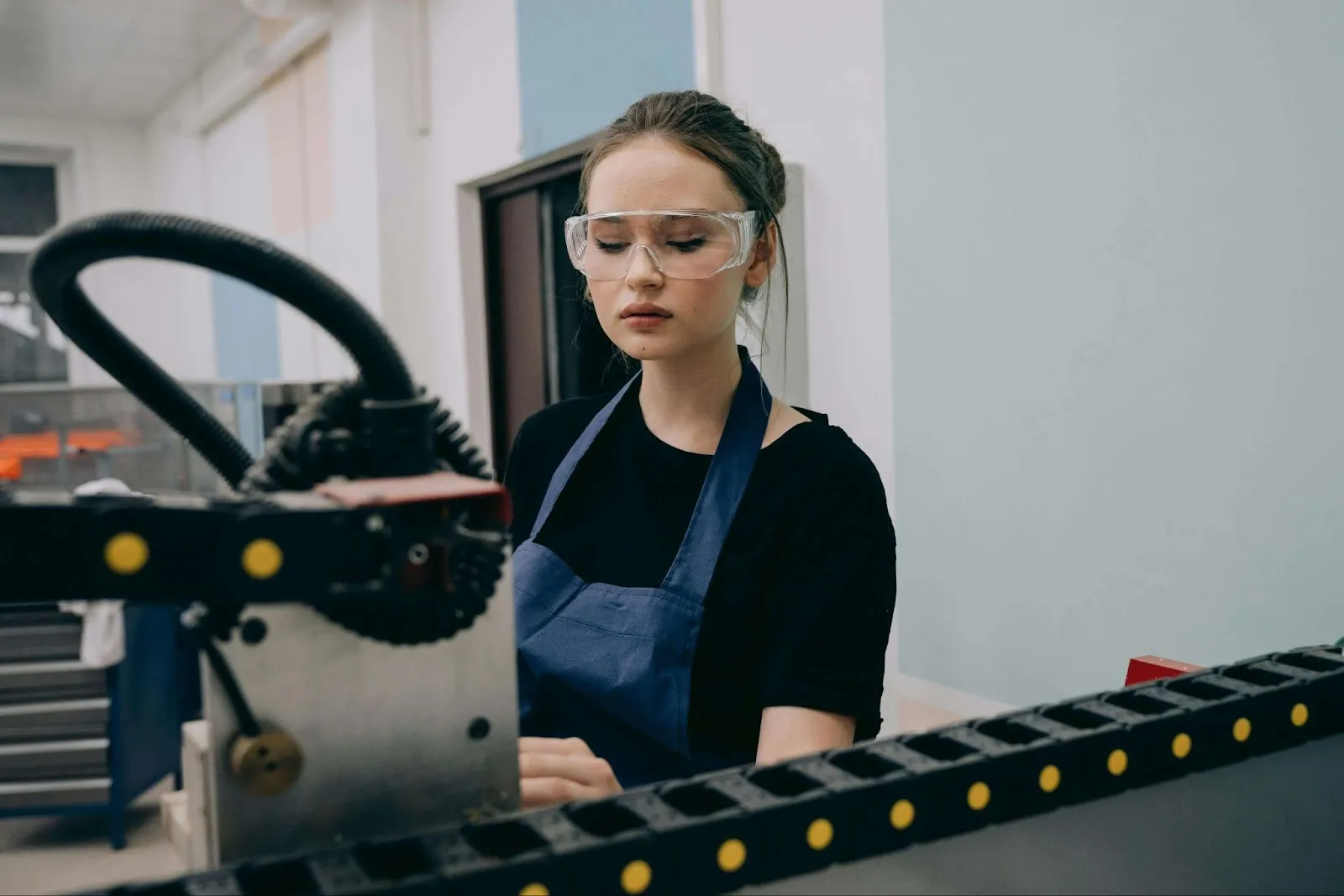
Why a smooth manufacturing onboarding process is essential
Nailing safety awareness is the hallmark of an effective onboarding process. It leads to a positive work environment and ensures your new manufacturing employees know and have what they need to succeed.
A few benefits of a successful onboarding plan can include:
- Integrated alignment: A solid onboarding program helps each new employee connect with the company’s goals, values, policies, and expectations.
- Faster time to productivity: When you provide new employees with everything they need on their first day, they can jump in and contribute sooner.
- Improved employee engagement: Your onboarding process acts as a first impression. When new team members feel valued from the start, employee retention and engagement improve.
- Bridged skills gaps: Onboarding is also the perfect time to invest in workforce development opportunities. Doing so can help you fill skills gaps within your current workforce.
9 manufacturing onboarding best practices
While manufacturing companies and work environments are all set up differently, some core onboarding strategies work consistently across the board. Following these best practices can help new hires get up to speed faster and lead to better results.
Develop clear quality standards and procedures
Before you even think about developing an onboarding process, you must be clear on your internal quality standards and procedures. Creating training materials around poorly defined internal processes is a recipe for confusion, and new hires may see it as a red flag.
Audit your current safety, regulatory, human resources, and operating procedures to ensure they’re clear and up to date. You can also take a pulse check by sending out a company-wide survey to gauge how current employees feel about compliance and its enforcement in their work environment. The survey could help uncover any communication disconnects between employees and leadership.
Choose training methods wisely
Delivery format is one of the first major decisions you’ll make when building your manufacturing training program. You have to decide whether to use in-person or online training (or a combination of the two) and what each format might look like.
There’s no universal answer to which type of training is better for learning—each has pros and cons. But since many jobs in the manufacturing industry typically involve hands-on work, many companies use a strategic mix of in-person and online training.
For example, a manufacturing company may cover standard operating procedures (SOPs) in person to demonstrate each step as it’s completed, while assigning an online course to cover human resources policies. Using both methods to cover key information can help reinforce critical details.
Create a consistent onboarding schedule
It can feel like there’s a lot to stay on top of when you’re starting a new job. The easier you can make it for your new employees to know what’s expected of them and when, the better. This is especially true if they have multiple on-site training sessions to attend.
Create a positive experience by helping new employees stay organized with a training schedule and to-do list broken down by date. They’ll know exactly what to focus on and may stress less about the training schedule since they’ll have time to prepare for what’s ahead.
Facilitate safety training and certification
Safety training is the top priority of any manufacturing onboarding program, no matter the job or the new hire’s years of experience. Every organization has its own machinery, company policies, and potential hazards that new employees must know before they start work. You should tailor your training program to these unique factors.
Your company can share this vital safety information through training materials like your employee handbook—something employees can always easily get their hands on. To help reinforce the material, consider assigning interactive training modules with assessments that test what team members know about key safety protocols. Hosting live webinars that include a Q&A provides employees an opportunity to get their questions answered.
Provide equipment and process training
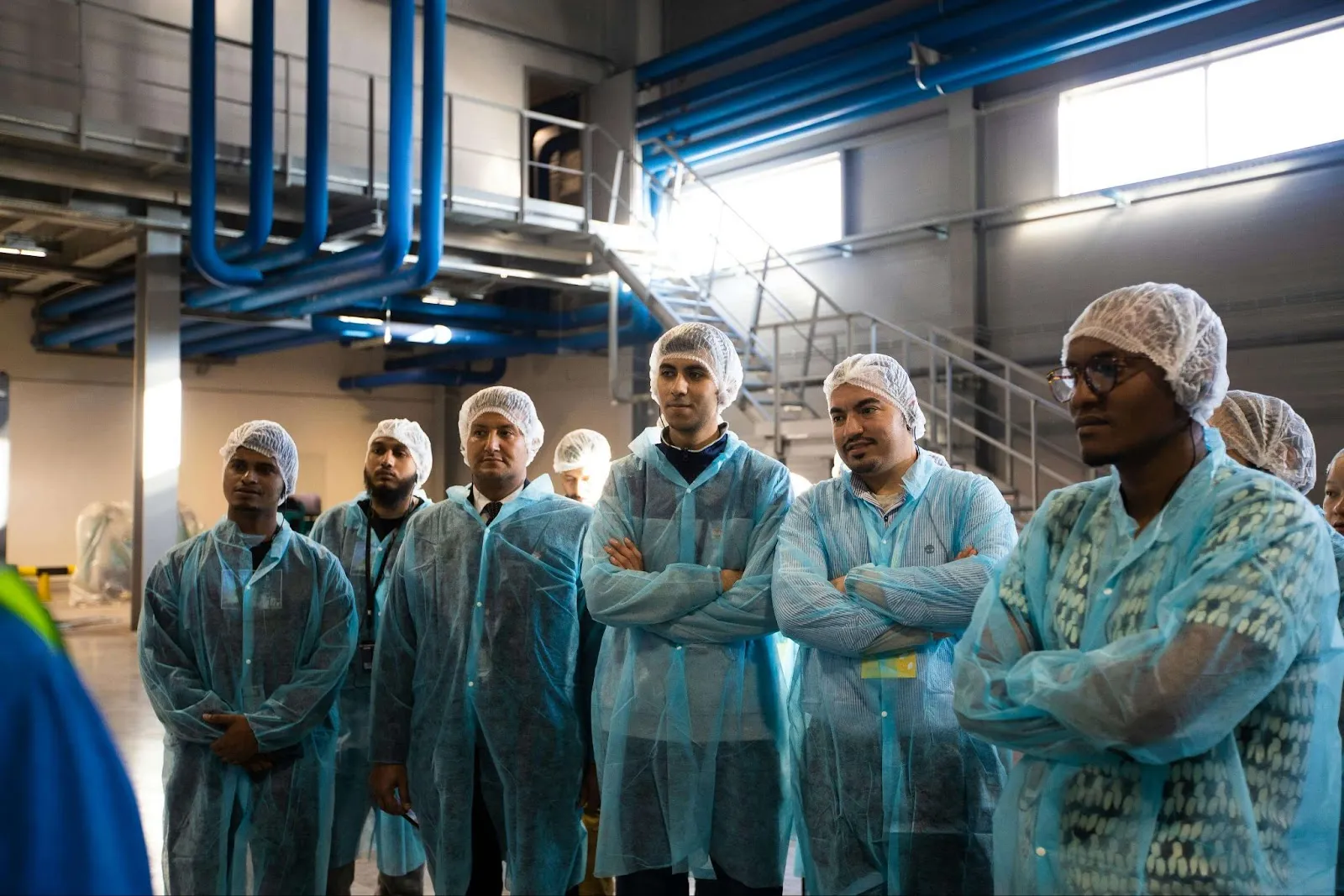
Because manufacturing companies have different hazards, their procedures and equipment are different, too. When it comes to your unique equipment and processes, training should be tailored to employees’ specific roles.
For example, if a team member’s job involves using a forklift, their training program should include a review of the forklift’s manual. This may also involve walking through your company’s SOPs for using the equipment.
Another thing to consider in this stage is personal protective equipment (PPE). If an employee is going to come in contact with hazardous materials, they need training on the type of PPE the company uses, how to wear it properly, and how to dispose of it safely. They’ll also need to know when and where they’re required to gear up.
Tailor training to the role
Once new hires complete basic onboarding tasks, they should receive training specific to their role. Here are a few examples of what that might look like for different manufacturing jobs:
- Production line worker: Assembly line workers should receive on-the-job training to learn how to operate machinery, assemble parts consistently, and maintain a clean work environment.
- Quality control specialist: These employees need to learn how to inspect raw materials for quality, conduct tests for product defects, and document results.
- Team leads or supervisors: Team leads need to know what to do when issues come up during production and ensure their team meets production goals safely and without breaking any rules.
Set performance expectations and KPIs
As employees settle into their new roles, they should have a clear understanding of performance expectations. That’s where key performance indicators (KPIs) come in. Employees and managers can track progress early on, and visible, tangible metrics can help motivate employees to hit certain targets.
The KPIs you set for new hires will vary by role, but there are a few goals to keep an eye on, including:
- Throughput: How quickly a production system generates finished products
- Cycle time: The time it takes to produce one finished product from start to finish
- Scrap rate: The percentage of defective products that are discarded
Schedule regular check-ins
Onboarding needs to be a two-way conversation. You want employees to feel comfortable raising their hands when they have a question or a problem. Scheduling regular check-ins during the onboarding process is a great way to encourage open communication and see how things are going.
Take advantage of check-ins to clarify information new hires may have missed or not understood. You can also use this time to build rapport and help new employees feel welcome. Fostering a sense of belonging can boost job satisfaction and reduce employee turnover.
Use technology that complements and streamlines your process
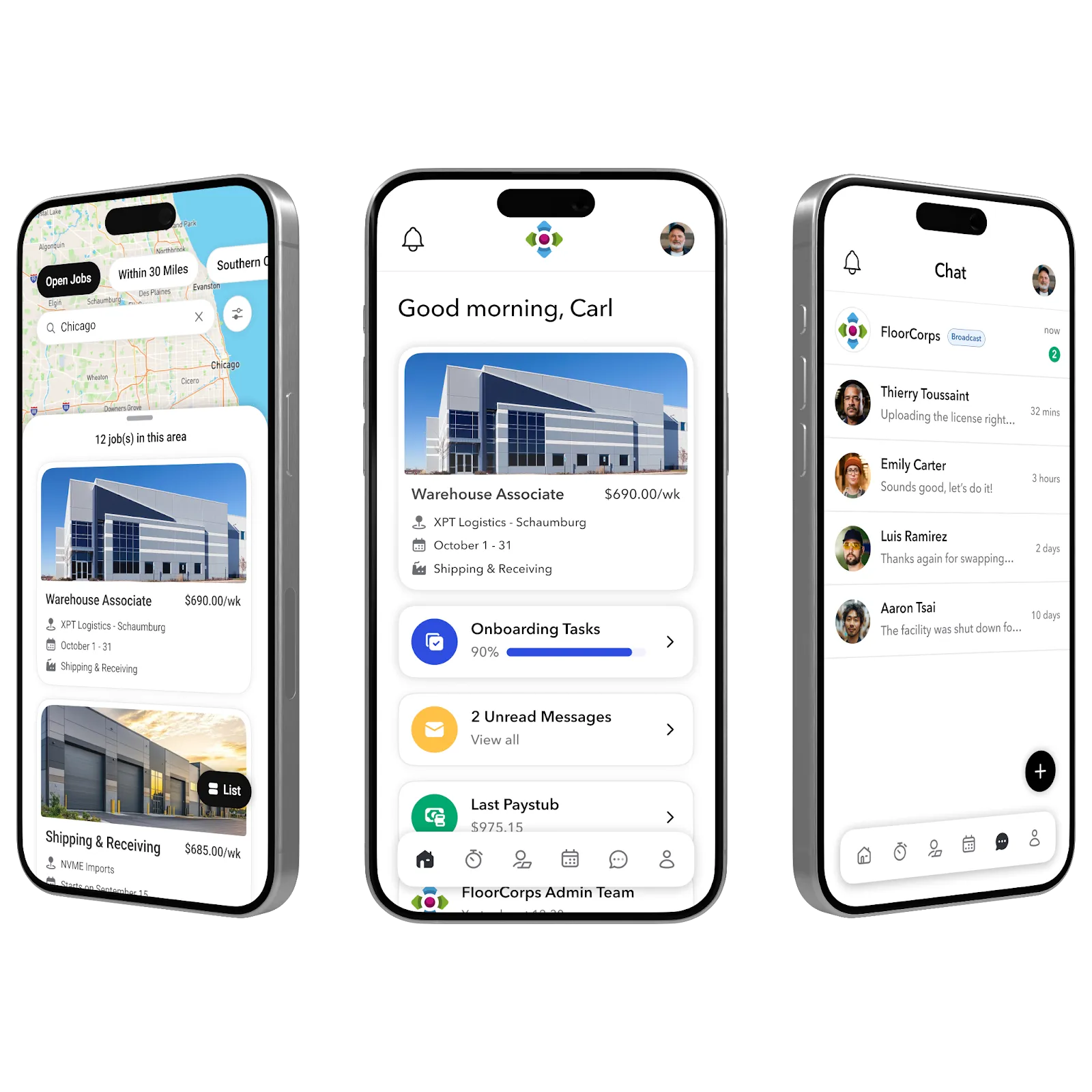
Onboarding can take a huge administrative toll on manufacturing companies, as each new hire costs a fortune in paperwork, training, and IT setup. While having a robust onboarding program is a must in the manufacturing industry, using technology to automate some of those steps can save you time and money.
Many companies use workforce management software to help them and their employees stay on top of onboarding tasks and check off all HR requirements. For example, some manufacturing companies use Teambridge to offer their employees a custom onboarding experience with a white-label mobile app. Employees can upload documents, check off tasks, view their schedule, and communicate directly with their teams. They can also use the app to clock in and out.
A mobile app is a game-changer for manufacturers—staff can pull it up right at the jobsite. Because of its accessibility and other features, technology can help streamline your onboarding process, keep it consistent, and ensure all employees have the information they need at their fingertips.
Implementation strategies across manufacturing environments
Because manufacturing is such a broad category, a single “best” approach to implementing onboarding strategies is unlikely. As you prepare to launch your program, consider these factors:
Facility-specific customization approaches
Your employee onboarding materials should reflect the unique aspects of the employee’s work location, especially when covering critical safety information.
For example, OSHA requires that employees who come in contact with hazardous chemicals must know exactly where each chemical’s Safety Data Sheet (SDS) is stored—a detail that varies by facility. Because of this mandate, consider adding an in-person or virtual facility tour to your onboarding process.
Shift and team-based considerations
Even when companies have standardized operating procedures in place, processes may vary slightly between teams. For example, while your company’s main communication channel might be email, some teams may use an instant messaging app for quicker communication during each shift.
For large companies, it’s helpful to clearly state that the new hire’s department lead will walk them through the day-to-day needs of their role to avoid conflicting information.
Scaling for multi-location operations
If you employ team members across multiple locations, consider creating a virtual training program to cover high-level information, such as the company’s mission and basic safety training. Then, follow up with facility-specific training.
This strategy allows employees to receive a consistent, company-wide onboarding experience that’s supplemented with the location-specific information they need to know.
Is your manufacturing onboarding process working?
Continuously monitor your onboarding process to see whether new initiatives are working. You can review the effectiveness of your onboarding by tracking key performance indicators like the following:
- Incident rate: The number of work-related injuries and illnesses per 100 full-time employees within a defined period
- Retention rate: Changes in the percentage of employees staying with your company over a certain time period
- Employee satisfaction: How employees feel about company culture based on data from routine pulse surveys that provide a feedback loop for continuous improvement
How to simplify your manufacturing onboarding process
You can build a powerful onboarding program with these manufacturing onboarding best practices. But with the right technology, your program can become even more robust.
Teambridge empowers you to create onboarding workflows tailored to different production environments, job roles, and skill levels—all without expensive customization. You can ensure consistent standards and accommodate the specific training required for various manufacturing processes, equipment, and safety protocols.
Let’s schedule a personalized demo so you can see how we can help you onboard staff at record speed and cut administrative costs without sacrificing quality.